Corrugated Steel Structure (CSS), which was applied in North America in the early 1900s and has been installed in more than 1,000,000 places worldwide, has been in service since 1996, 100 years later, in Korea with POSCO, Korea Expressway Corporation, Seoul National University, Hanyang University, etc. It has been applied to the domestic market through commercialization research by specialized companies. Based on this, since the 2000s, it has been widely applied to road crossing passages, waterways and local small rivers, animal movement ecological passages, and Piam tunnels. Based on the advantages and economic feasibility of minimizing the existing vehicle traffic control during construction, it is a universal new construction method along with the existing reinforced concrete construction method. About 5000 corrugated steel plate structures have been installed and operated in Korea for 20 years.
However, regarding the various advantages of the construction method and the rapidly occurring demand, in the beginning, detailed explanations of the national design standards and specifications were insufficient. Problems such as deformation of the corrugated steel sheet occurred intermittently due to the lack of understanding of the backfill material and backfill compaction, which are the most important factors in
To improve this, ChungAmEnC has continuously improved and supplemented related standards through R&D with various related organizations, and based on domestic and foreign failure cases, provides optimized design solutions in advance for possible problems during actual construction. Optimized solutions include Virtual Construction: a three-dimensional system for step-by-step forecasting processes. (BIM LoD: 350 / Tekla, Trimble) and 3D Scanning (Leica P30 System, Cyclone ) Minimize errors that may occur at each construction stage I did. In addition, by providing 3D FEM, 3D printing and landscape design solutions, we will do our best to become a company that continuously develops and provides the world's best solutions that overcome the uncertainty of design and construction anxiety that customers have felt.
History of CSS
In 1896, an American civil engineer James. H. Watson and Starting with Stanley Simpson's patent, it was applied to small drainage channels in North America until the 1930s, and by the late 1900s, the maximum span was applied up to 11m and expanded to small bridges, passageways, and military facilities (ammunition depots). Since the 2000s, the span has been extended to 23m and applied to ecological tunnels, mine stockpiles, reclaim tunnels, and military facilities (hangars). 2014-2016 R&D and commercialization of extra-corrugated corrugated steel sheet (EXSCor) of Cheongam EnC With success, the maximum span was extended to 40m. It satisfies the maximum loads of CAT 797F (about 620 tons), EURO LM71, mine trucks, which could not be applied in the past with respect to live loading along with the expansion of span, so that it is economical, stable, and workable than concrete structures in multi-step processes. has enough competitiveness. In addition, extra corrugated steel sheet (EXSCor) is listed as a construction method and product according to design standards in Korea (KDS, KCS) as well as AASHTO LRFD and ASTM A796M in the United States.



Solution Tunnel & Underpass



Advantages of corrugated steel plate application (open tunnel, passage, waterway)
As Korea enters an aging society, the aging of construction workers has accelerated, and as of 2018, 6 out of 10 people are over 55 years of age. Also, among the safety accidents that occur during the construction of reinforced concrete structures at civil engineering sites, there are safety accidents in which the formwork fails to withstand the pouring pressure and collapses during concrete pouring. In the design of Dongbari considering the casting pressure of the formwork, the bearing capacity of the actual construction site must satisfy the design requirements, but in reality there are many difficulties. Recently, construction companies have been working hard to secure the installation stability Redesign is required, and in the event of a safety accident, responsibility is being held.
In particular, when constructing a waterway box with a small cross section, a very dense copper bar must be installed for the installation of the bar, and the working environment for construction workers is inevitably very poor. This has a problem that can lead to safety accidents due to fatigue of aging workers.
Corrugated steel sheet has economical and eco-friendly advantages, and there is no formwork or copper construction for concrete pouring. Compared with the reinforced concrete method, the number of construction workers is reduced by up to 80% or more , so safety accidents are prevented and construction is decreasing. It has the advantage of redeploying the workforce.

Corrugated Steel Culvert and Waterway (Underpass)
Road culverts are frequently designed not only in general design but also in emergency construction such as flood restoration, and there are many similar tasks in applying the design, so a reasonable standard design was presented in consideration of structural stability. Introduction has been reviewed. After the first application of the corrugated steel plate underground structure to the Jungang Expressway in 1997, “underground steel plate structure design and construction guidelines”, “corrugated steel plate culvert standard drawing” and “corrugated steel plate waterway culvert standard drawing” established by the Korea Highway Corporation Road Traffic Research Institute in 2001 ” has been enacted and applied. Compared to the existing standard concrete culvert 4.5m by 4.5m, the corrugated steel plate culvert consists of a semi-circular arch and a high-arch (W-type) span of 6m to 6.25m. This makes it possible for vehicles to cross within the culvert, which was not possible with concrete culverts, and there are about 500 in use in Korea.


Due to the design and construction using the road construction standard diagram in the application process, various situations and conditions (skew, flat earth pressure, drainage, foundation design, backfill management, etc.) were not taken into account. Although the design and construction were changed to suit the site conditions and circumstances, the need for specific design guidelines for structure design emerged, and in terms of construction, it was necessary to improve the material, scope, and construction method of the backfill and to improve the drainage problem. has been

Solution
The major problems of “standard corrugated steel sheet” used mainly in small structures such as road culverts are cross-sectional deformation exceeding the standard (permissible displacement of 5%), local buckling failure, tearing of bolt joint steel plate, bolt joint leakage, and deformation of the end. As a solution for Daehan solution, the secondary moment of cross-section is increased by 8~9 times, “extra-bone type and super-bone type (EXSCor)” We have the technology to manufacture corrugated steel sheets that can compensate for the above problems (permissible displacement 2%, super corrugated steel 1%) by using “corrugated steel sheet”.
1) By changing the foundation form from retaining wall type to block type in the direction of improving the vertical cracking and activity of the foundation concrete, which was a problem in the concrete foundation, the total weight of the structure is reduced to solve the problem of unequal settlement,
2) In case of leakage in the connection between the corrugated steel plate and the foundation, a leak prevention method was additionally installed at the top of the foundation to prevent condensation and influent water from stagnating.


3) When selecting a section, if there is room from the top of the structure to the planned height, an Arch Shape section with excellent openness can be applied.
4) Simplify the process (Step 3 ➞ Step 2), the construction period is reduced by 30% compared to the existing method, and the construction cost is also reduced by more than 15%.









Corrugated steel sheet cut-out tunnel CSS Tunnel
When the width of the road increases in the corrugated steel plate tunnel (when the total effective width is more than 20m), a double structure is applied in consideration of the rigidity limit of the corrugated steel plate structure and the construction conditions. In case of construction during public use, some lanes must be inevitably controlled for vehicle traffic, and the foundation is installed on the road median, so there is a disadvantage of having to expand the width of 4 lanes in the tunnel connected to the existing lane. As a solution to this, by applying EXSCor corrugated steel sheet, it is possible to construct with two or shorter spans maintaining the existing lane.

ChungAmEnC@Copyright








Solution
EXSCor corrugated steel sheet is the world's largest corrugated steel sheet with the world's greatest rigidity, while the material increases by 8-9% by increasing the width and depth of the corrugation compared to the existing corrugated corrugated steel sheet. If EXSCor corrugated steel plate is used, rigidity can be secured only with the main plate (without reinforcing plate) for a span of 24m. As there are no processes such as assembly and en-cased concrete pouring, construction is easy and construction costs are reduced. If the reinforcing plate is used in the super-frame type, it can be applied up to a span of up to 40m, and it can be crossed over a short span without installing a foundation on the 8-lane road median, so it can be constructed while maintaining the traffic flow of the existing road.



ChungAmEnC@Copyright




ChungAm EnC@Copyright

ChungAm EnC@Copyright


ChungAmEnC@Copyright

ChungAmEnC@Copyright
Downtown construction applicability
without interrupting the flow of vehicle traffic, There is no need to resolve civil complaints and bypass roads due to traffic congestion due to the bringing in of materials during construction in downtown areas. (Perforation method: 90% reduction compared to rebar, ready-mixed concrete and precast vehicles)


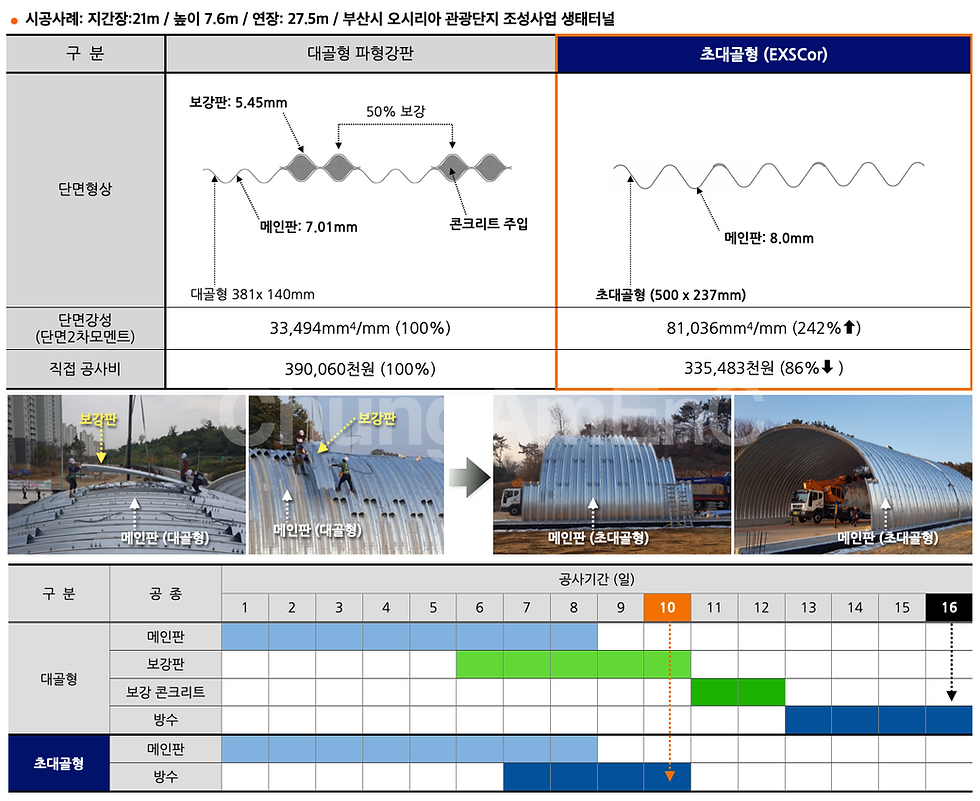
Curve section & Skew applicability
When applying the curved section, the 'Built-Up Beam Elbow' pre-fabricated in the factory is used for construction by bolt assembly on site. By maintaining the road alignment as much as possible in vehicle drivability and visibility. It is superior to general concrete structures. As the inlet and outlet skews are also pre-processed and manufactured in the factory, fast construction is guaranteed by bolt assembly on site. In addition, Cheongam ENC introduced the world's first BIM design technique down to the details to 'zero' errors in production and field.
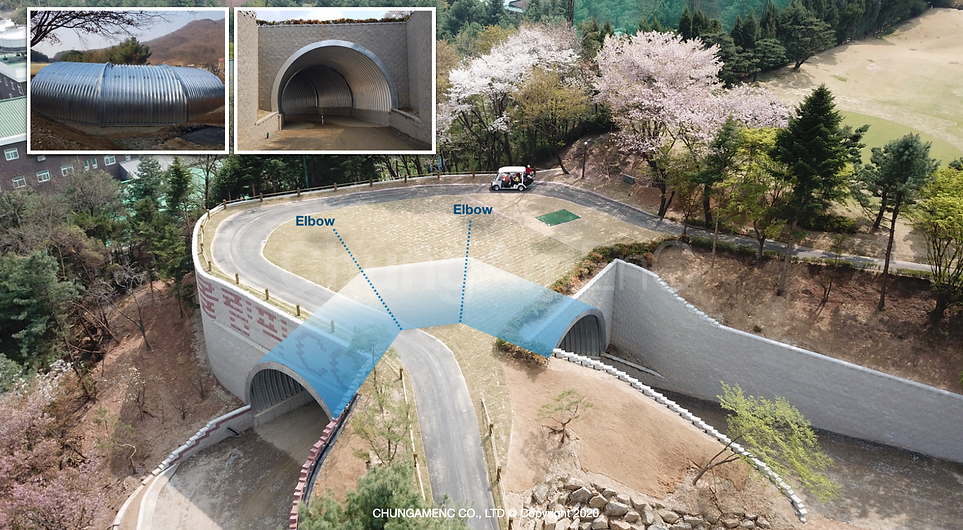

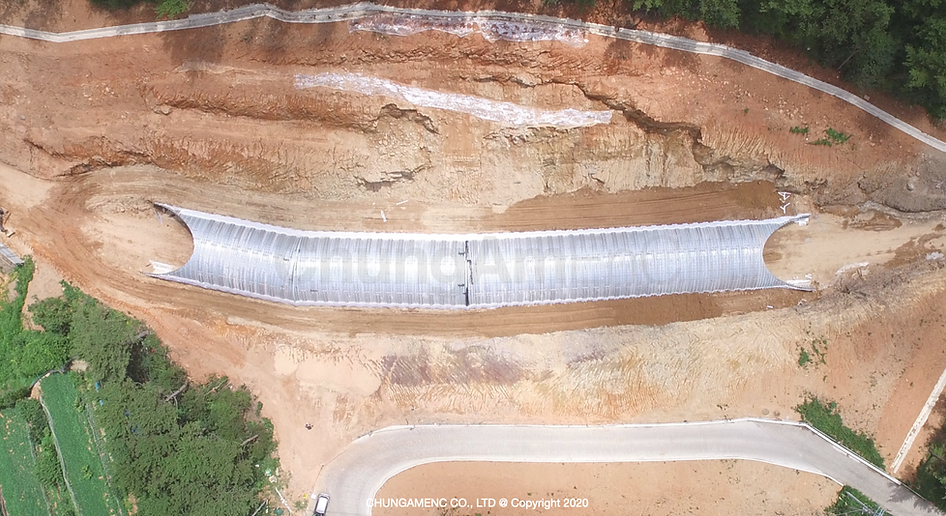








Construction cost reduction application case
Despite the change of backfill material from sub-base material to ➞ subsoil (compactness 95% ➞ 90%), the safety factor of corrugated steel plate increased high, and the displacement during construction was managed to less than 0.05% (2% based on KCS allowable displacement) Existing ribs Compared to the type (380mm by 140mm / 400mm by 150mm), the backfill construction cost was reduced by 72%. LG LED P10 , May 2016

Minimum Corrugated Steel Sheet Combination
By composing a cross-section that can be installed with a combination of 2 to 4 sheets of corrugated steel plate (380mm by 140mm) , we developed a combination that can be applied to emergency construction and high-fill sections . In addition, the maximum cover height was calculated according to the backfill material (sub-base material, subgrade soil) and the degree of compaction (85%~90%). As two corrugated steel sheets can form a circular cross section of 1.8m to 3.0m, the number of bolts is reduced by 36% compared to the existing standard corrugated steel sheet combination, thereby securing assembly and construction period, improved waterproofing performance and economic feasibility.

Corrugated steel plate installation
For corrugated steel plate, if there is a foundation, check the foundation bearing capacity presented in the design drawing (piling if necessary), pour the footing concrete, and install the foundation concrete on it. When constructing the foundation concrete, install the base channel connected to the corrugated steel plate on the reinforcing bar. After the base concrete is cured, fasten the corrugated steel plate and the base channel with bolts and nuts.
Assemble the corrugated steel sheet according to the order by checking the markings marked on the inside and outside of the corrugated steel sheet and BP0-00S marked on the drawing. If the end-treatment is a concrete face wall, backfill is performed by securing the compaction material and compaction rate specified in the specification after completing the concrete face wall by fastening the anchor bolt and reinforcing bar of the face wall. Before backfilling, waterproof the bolts specified in the drawing and between the corrugated steel plate and the corrugated steel plate with gaskets and waterproof caps. In case of bevel, after waterproofing and backfilling process, the bevel part is finished with Ring-Concrete.

CSS_Headwall Type
ChungAmEnC@Copyright

CSS_Bevel Type
ChungAmEnC@Copyright

En_Cased Concrete Stiffener Procedure_2019
Patents Registered
10-0512522, 10-0609125, 10-1829819, 10-0448015, 10-0622059, 10-0634019, 10-0799979, 10-0837212, 10-0842029, 10-0875250, 10-0875251, 10-1599811, 10-1620515, 10-1629291, 10-180105 3
